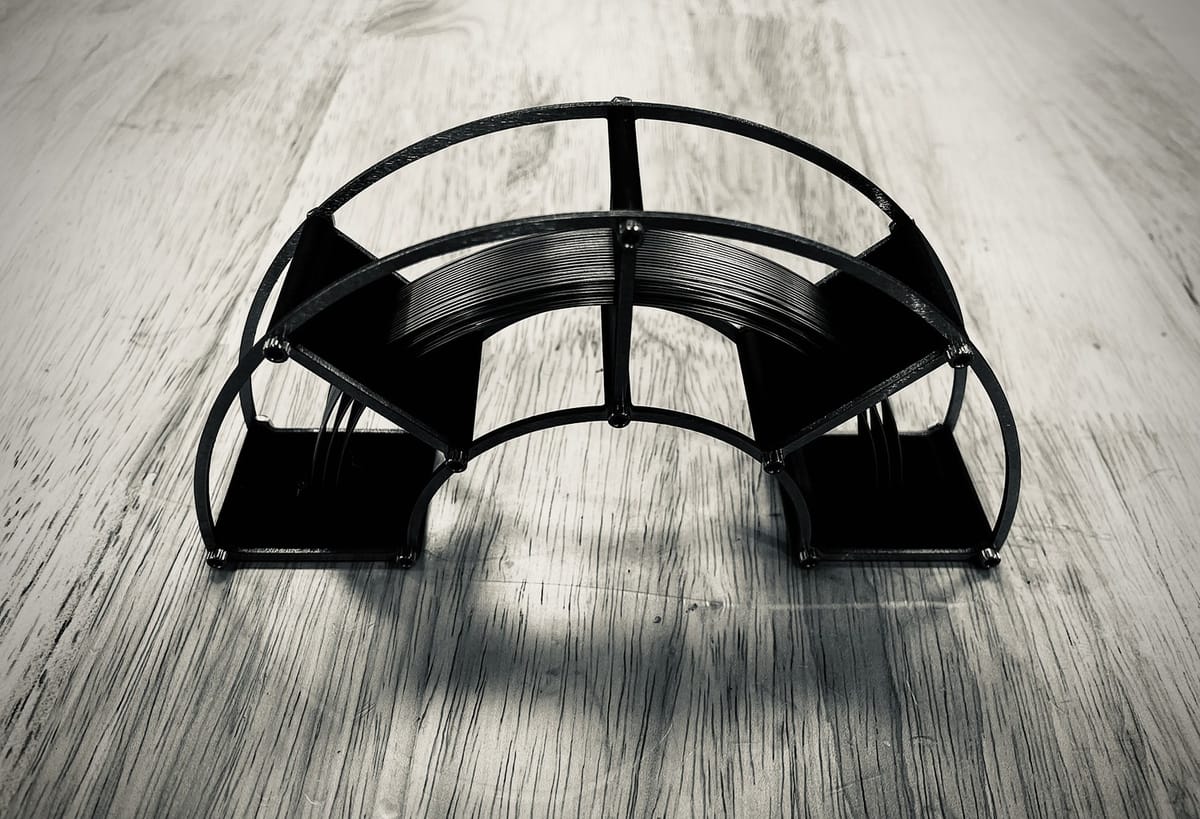
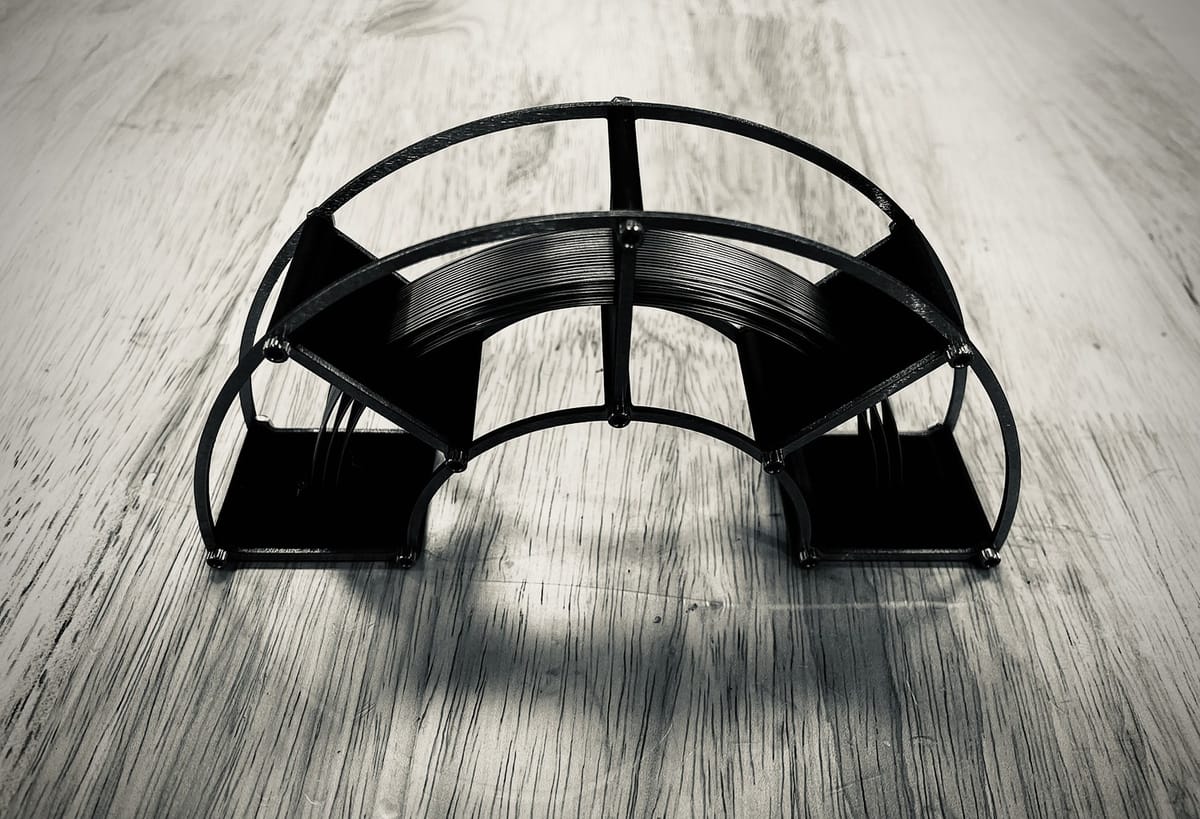
Today St. George-based Intergalactic announced it has applied its proprietary, patented Boreas3 microtube heat exchanger technology to curved designs to conform to the complex, cylindrical shapes found on aircraft fuselages and engines.
The novel patent-pending curved designs are the product of Intergalactic’s ongoing internal research and development to invent, improve, and commercialize thermal technologies for modern air and space applications. Intergalactic’s patented laser welded microtube heat exchangers have been in high demand, and the curved designs unlock new opportunities to conform to non-rectangular spaces. Matching heat exchangers to existing complex surfaces drastically increases spatial volume utilization and thermal exchange efficiency in otherwise difficult or unusable locations.
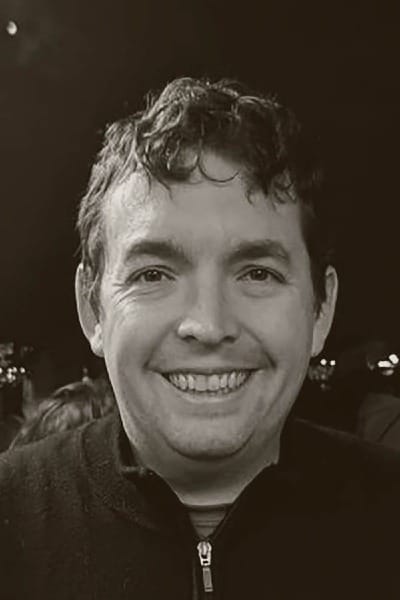
“Most of the time, designing heat exchangers for curved spaces is literally like trying to fit a square peg in a round hole,” said Intergalactic CTO Nick Kaiser. “If you’re building an aircraft engine, for example, the nacelles are going to be cylindrical in shape, which presents a basic geometry problem for installing critical heat exchangers. By developing the technology and manufacturing processes to apply curved design to our laser welded microtube heat exchangers, we’re opening a new world of efficient cooling options for airframers and engine makers in defense and civil aviation.”
The curved design offers many technical advantages for installation in cylindrical spaces, including:
- Enabling greater thermal exchange density by using available space more efficiently than typical rectangular designs
- Removing the need for blocker plates to close gaps between rectangular heat exchangers and rounded surfaces
- Maximum space efficiency while minimizing weight
- Increased shell-side flow
“There’s a large and growing market demand for curved heat exchangers, especially those that can offer substantial size and weight savings compared to the legacy plate-fin heat exchanger technology,” said Kaiser. “Our patented approach to laser welded microtube heat exchangers has already shown tremendous advantages over the aging plate-fin standard, which increasingly faces obsolescence in aerospace. We’re excited to take the next step by applying our proven technology to curved designs.”
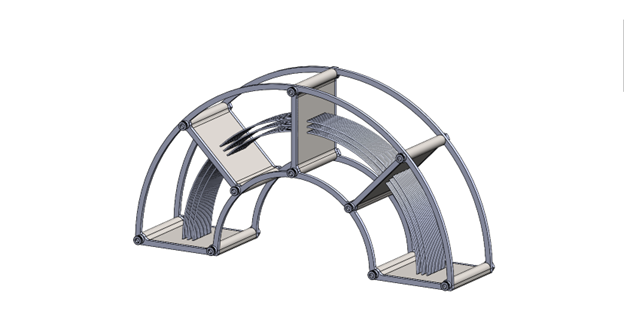
Intergalactic was the first company to fully flight qualify a microtube heat exchanger on a major military platform. After a series of successful flight tests in the summer of 2023, the company achieved a technology readiness level 9 (TRL 9) for its heat exchanger and other system components. Previously, Intergalactic was granted a U.S. patent for its proprietary laser welded microtube heat exchangers for aviation and space in late 2022.
Intergalactic’s R&D design and manufacturing engineers will continue refining the general characteristics of the curved microtube heat exchanger while working in parallel with industry partners to apply this underlying technology to real-world technical applications.
To inquire about the curved microtube heat exchanger, email phonehome@ig.space.